The Ultimate Guide to Final Drive for Excavators
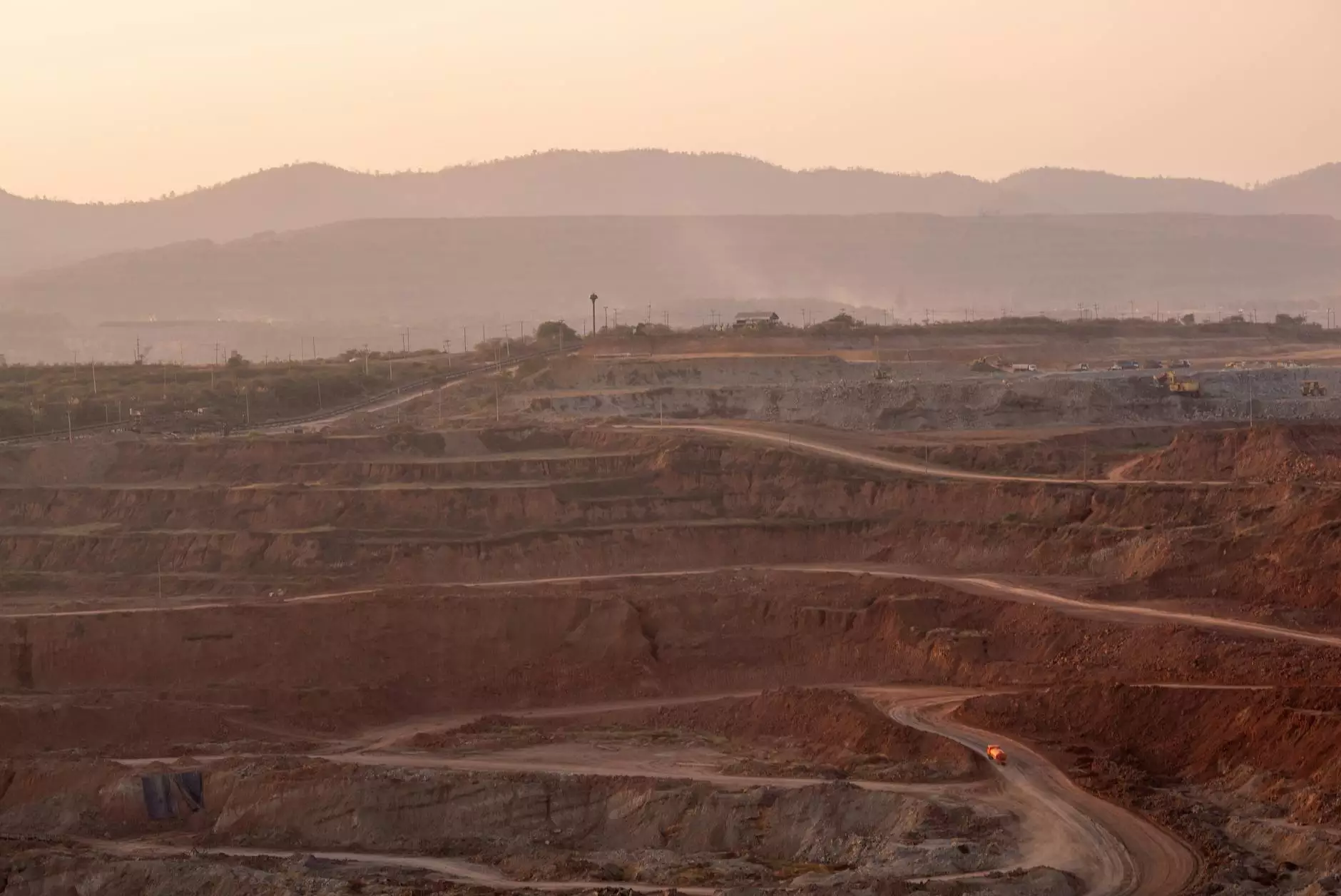
Excavators are essential in the construction and excavation industry, providing unmatched efficiency and power. One of the critical components that contribute to an excavator’s functionality is the final drive. In this comprehensive guide, we will explore the importance of final drives for excavators, their components, types, maintenance, and how to choose the right one for your needs.
Understanding Final Drives
The final drive is a crucial part of an excavator’s drivetrain that transfers power from the hydraulic motors to the tracks, enabling the machine to move and operate effectively. It usually consists of several key components, including gears, bearings, and hubs.
Components of a Final Drive
A typical final drive for excavators consists of the following parts:
- Hydraulic Motor: Converts hydraulic energy into mechanical energy.
- Reduction Gears: Reduces the speed while increasing torque to the tracks.
- Bearings: Support the rotating components, ensuring smooth operation.
- Hubs: Connect the final drive to the tracks, allowing for movement.
Importance of the Final Drive
The final drive plays a vital role in the overall efficiency of an excavator. Here are some reasons why it is crucial:
- Power Transfer: It is responsible for transmitting the hydraulic power to the tracks, thus enabling movement.
- Torque Multiplication: The reduction gears within the final drive multiply the torque, allowing the excavator to handle heavy loads.
- Durability: A quality final drive ensures the longevity of the excavator, as it withstands heavy wear and tear.
- Cost Efficiency: By maintaining an efficient final drive, you can reduce operational costs related to fuel and repairs.
Types of Final Drives
There are various types of final drives suited for different excavator applications. Let’s break them down:
1. Planetary Final Drives
Planetary final drives are commonly used in excavators due to their compact design and efficiency. They consist of a central sun gear surrounded by multiple planet gears, providing excellent torque multiplication and reduced size.
2. Spur Gear Final Drives
Spur gear final drives utilize straight-cut gears to transfer motion. While they are less common than planetary drives in excavators, they offer simplicity and are easier to maintain.
3. Bevel Gear Final Drives
Bevel gear final drives are used when a change in direction of power transfer is necessary. They are effective in providing high torque and altering the axis of rotation.
Choosing the Right Final Drive
Choosing the appropriate final drive for excavators involves several considerations:
1. Excavator Size and Weight
The size and weight of your excavator will significantly influence the type of final drive you need. Larger excavators generally require more robust and powerful final drives.
2. Application Purpose
Consider the primary application of the excavator. If you are engaged in heavy lifting or excavation work, a final drive with higher torque capabilities may be necessary.
3. Terrain Conditions
Different terrains, such as rocky or muddy grounds, require different levels of traction and power output. Make sure to select a final drive capable of handling the expected conditions.
4. Manufacturer and Warranty
Always choose final drives from reputable manufacturers to guarantee quality. Ensure that there is a warranty, as this will provide assurance regarding the durability of the component.
Maintenance Tips for Final Drives
Regular maintenance is crucial to ensure the longevity and efficiency of your final drive. Here are some essential maintenance tips:
1. Regular Inspections
Inspect your final drive frequently for signs of wear, leaks, or damage. Early detection can prevent costly repairs.
2. Lubrication
Ensure that the gears and bearings are regularly lubricated to minimize friction and heat. Use high-quality lubricants that are compatible with your final drive.
3. Monitor Operating Temperatures
High operating temperatures can indicate issues within the final drive. Monitor temperatures during operation and address any abnormal readings immediately.
4. Cleanliness
Keep the final drive area clean to prevent dirt and debris from entering the system, which could lead to premature wear.
Conclusion
Understanding the significance of a final drive for excavators allows operators and owners to make informed decisions when it comes to maintenance, repairs, and replacement. By ensuring you have a quality final drive, you enable your excavator to perform effectively, reduce operational costs, and extend the life of your machine.
For more information on high-quality final drives and excavator parts, visit Shop Hydraulic America. Our extensive range of auto parts & supplies and motorcycle parts & supplies ensures that you can find everything you need to keep your machinery running smoothly.
Investing in the right final drive not only maximizes your excavator’s performance but also contributes to overall operational efficiency in the demanding world of construction and excavation. Make the right choice today, and keep your excavators moving forward!